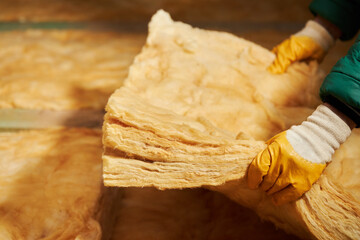
Insulation Perth is a material that reduces the flow of heat. This prevents energy loss and saves money on utility bills.
Fiberglass is widely used and available at home improvement stores. Mineral wool like Greenfiber is sustainable and uses a low-energy manufacturing process. Cellulose and spray foam insulation are blown in place with special equipment.
Insulation Materials
Insulation materials are designed to reduce the flow of heat between objects by reducing thermal conduction, reflecting thermal radiation and blocking air movement. There are several different types of insulation materials available to homebuilders, each with its own unique characteristics and performance.
The most popular form of insulation material in the United States is fiberglass, which comes in a variety of products including blankets (batts or rolls) and loose-fill insulation. It is also available as rigid foam board and duct insulation. Fiberglass has excellent acoustic properties and is non-flammable. It is typically installed by professional installers who are skilled at achieving the correct density and R-value.
Blanket insulation consists of flexible fibres, most commonly fiberglass, but also mineral (rock or slag) wool and plastic fibers. These are generally blown in place or fitted between wood-frame studs, joists and beams using special equipment. Some come faced with foil or Kraft paper which serves as a vapour barrier. These products are effective in new construction, and may be suitable for retrofitting into existing homes with attics, crawl spaces or rim joists.
Polyurethane foam is growing in popularity as a spray or foamed-in-place insulation. It is also available as laminated insulation panels with a variety of facings. The sprayed and foamed-in-place application of polyurethane is more cost efficient than installing foam boards, because the liquid foam moulds itself to any surface. All closed-cell spray polyurethane used today uses a non-HCFC blowing agent.
Foam insulation can also be poured in place, and is often used in insulated concrete forms (ICFs), which create a house that is sturdier than traditional stick-built homes and is highly energy efficient. These are typically built by a specialist contractor but are also an option for do-it-yourself builders who choose to follow manufacturer and safety precautions carefully.
Loose-fill insulation consists of a wide variety of materials, including cellulose, fiberglass, vermiculite and perlite. These are generally blown in place or poured by experienced professional installers who know the appropriate density and R-value. This type of insulation is effective in enclosed cavities such as walls and attics, and is also useful for filling gaps and crevices.
R-Value
R-Values rate how well a particular insulation material can prevent the flow of heat into and out of a home or commercial building. Understanding this rating system can help property owners make better decisions when choosing materials for their insulation projects, and maximize the effectiveness of their investment.
A material’s R-Value is determined by dividing its thickness by its thermal conductivity, with the result being a number that measures its thermal resistance. The higher the R-Value, the more effective an insulation material is at blocking the flow of heat.
Generally speaking, higher R-Values are used for walls and roofs and lower R-Values are used for floors. However, this is not always the case, as other factors can influence the R-Value of an insulation product as well.
Most insulating products work by trapping pockets of air within them. This air acts as a barrier to the movement of heat, so that when hot temperatures rise, they have to travel much farther to reach a cooler area, and the insulated material keeps them trapped in place. As a result, the heating and cooling systems don’t have to work as hard to maintain comfortable indoor temperatures, which reduces energy costs over time.
When comparing the R-Value of various insulating products, it is important to keep in mind that the advertised R-Value is usually the new R-Value that is quoted by the manufacturer. The R-Value of a blown-in cellulose or fiberglass insulation, for example, can vary based on the thickness and density of the material that is applied.
A blown-in R-Value can also change over time, as the product settles. This is why many manufacturers advertise an R-Value that is a projection of what the insulation will achieve over a 15 year period.
It is important for inspectors to be familiar with the R-Values of different insulation materials, especially when inspecting a home or business or performing an energy audit. By learning more about the R-Values of different types of insulation, inspectors can provide customers with a clearer picture of what type of insulation would be most suitable for their project and how to get the most out of it.
Condensation
Insulation works by reducing the transfer of heat through walls, floors, ceilings and other interior components of a building. It is a layer of material that prevents warm air from leaving your house in the winter and cool air from coming in in the summer. Insulation is primarily used to reduce energy costs, but it also protects the structure of a building from damage and improves indoor comfort.
When deciding on the right insulation for your home, it’s important to understand how different materials impact condensation and moisture control. It’s also a good idea to partner with a reputable professional that can advise you on the best insulation materials for your home.
Condensation happens when warm air in your home meets cold surfaces such as exterior walls or drywall. This rapid cooling causes the moisture in the air to turn into water. The moisture can then dribble down the wall and cause major damage to the interior walls of your home. This type of condensation can lead to wood rot, mold growth and even structural failure.
Many common insulation materials such as fiberglass, mineral wool, cellulose and spray foam are susceptible to condensation. However, some newer insulation materials like polyurethane are designed to prevent the occurrence of condensation. This is achieved by adding a moisture barrier that prevents moisture from touching the insulation surface.
If you do experience issues with condensation, it’s best to get it sorted as quickly as possible. Persistent condensation can lead to the growth of mould that releases spores into your home. This can cause health problems such as asthma and allergies, compromising the health of your family. It can also result in weakened plaster and wallpaper that could collapse or peel over time.
Moisture trapped in a porous insulation system can also result in corrosion under insulation (CUI), which can eat away at the metal in the mechanical system that is being insulated. This can result in costly repairs or replacements. Proper insulation can help to minimise condensation by improving ventilation, maintaining optimal temperatures and ensuring the correct thickness of insulation is installed in your home.
Foam-In-Place
Foam-in-place is the ideal specialty packaging material for protecting delicate, high-value and sensitive products from the many bumps, shocks and pressures that occur during transit. The molded foam expands and molds itself to the item, securely cradling it in place while providing surface, shock and thermal protection. It also eliminates air infiltration and maintains product fidelity. Foam insulation is an excellent choice for insulating your home because it creates a barrier that blocks heat from escaping. It blocks a significant amount of heat energy from the sun and other sources of unwanted heat, as well. Foam insulation is available in a variety of forms, including spray foam and pre-fabricated foam panels, which are easily installed with staples or nails.
Foam packaging systems are a quick, efficient way to protect fragile items while improving warehouse productivity and reducing shipping costs. These systems are a great option for businesses that ship unique orders that require custom protective materials. They use a dispensing system that mixes liquid components of polyurethane foam to form a hard, protective encasing. These systems are easy to use and require less manual labor than traditional packing methods. Foam-in-place offers flexible solutions that adapt to each unique order, reducing waste and saving time.
As environmental concerns grow, customers are demanding that their goods arrive undamaged and unharmed from warehouse to doorstep. The need for a more sustainable packaging option is driving the shift from plastic foam-in-place products to paper packaging. Foam-in-place systems are a great option for companies that want to cut waste and improve sustainability, but they can’t replace the benefits of paper cushioning.
In addition to environmental concerns, consumers prefer the lightweight, curbside recyclable nature of paper over plastic. Paper is also safer to handle and doesn’t contain the toxins that many foam-in-place products do. Plastic foams are chemical based and can cause respiratory and skin reactions.
A recent study compared the performance of paper vs. plastic foam-in-place for a package job involving headlamps and other electronic equipment. The engineers sized the containers to density pricing, and the results showed that paper performed better than the standard foam-in-place. In addition, a paper pack was lighter than a plastic one and offered superior cushioning while saving cost.